Semi-Cryogenic Engine Test Stand
Business Motivation:
In 2019, there was a lack of regulations in India for private rocket engine testing, posing a major hurdle for Agnikul Cosmos. To bypass this, I designed a portable semi-cryogenic engine test stand, enabling hot-fire tests in remote locations with minimal restrictions.
Role and Responsibilities:
I owned the end to end developement of the thrust test stand from ideation till deployment, which included the load-bearing structure, sensor suite, plumbing, instrumentation, and NI DAQ system. Worked with the sub-system Lead engineers of the Launch vehicle to understand which perforamnce metric were needed and build a product roadmap for the Test Stand.
Challenges and Solutions:
- Navigating Undefined Requirements: With minimal existing documentation, I engaged directly with sub-system owners to understand their evolving needs over the next two years, translating them into a structured product roadmap.
- System Design & Modularity: Developed a turnkey, modular test stand capable of supporting a variety of propulsion tests while maintaining portability for flexible deployment.
- Engineering for Field Testing: Designed critical hardware, including a linear bearing structure that supported engine loads with a three-axis load cell, jet deflectors for safe testing, and a custom in-house electro-mechanical valve to reduce costs.
- Rapid Execution & Cross-Team Collaboration: Led requirement gathering and coordinated across multiple teams to accelerate the design cycle, successfully delivering a functional test stand within three months.
Impact and Results:
- Accelerated Engine Development: The modular test stand enabled rapid hot-fire testing cycles, significantly reducing propulsion system validation and iteration turnaround time.
- Scalable Testing Infrastructure: The test stand was designed with modularity in mind, ensuring it could be adapted for future semi-cryogenic engine iterations, providing long-term usability and flexibility.
- Secured Funding: The successful acquisition of high-quality propulsion data directly contributed to securing a $3.2 million seed funding round by raising the TRL levels of the hardware.
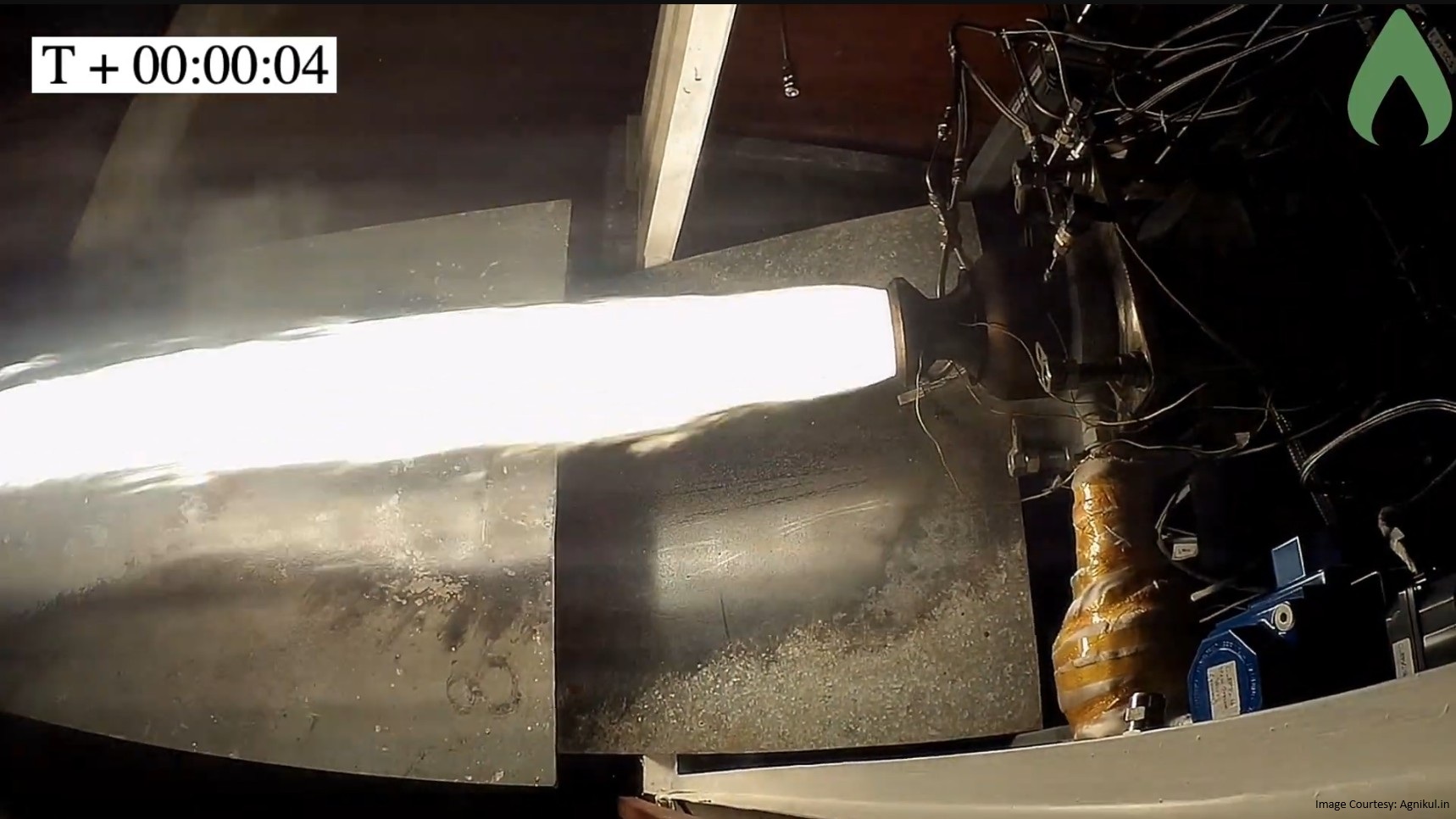
Service Tool for SparkCharge
Business Motivation:
SparkCharge's early core products, the V1 and V2 Roadie, faced significant field deployment challenges. Due to early-stage design limitations, these chargers frequently encountered issues that could only be resolved by dispatching service technicians, leading to high operational costs and reduced customer satisfaction. The company needed a cost-effective and scalable solution to diagnose, troubleshoot, and fix these chargers without requiring on-site service calls.
Role and Responsibilities:
- End-of-Line Charger Test System: Developed a factory-based test system to identify and eliminate defects before chargers left the facility, reducing post-deployment failures and minimizing the need for field repairs.
- Remote Service Tool: Designed a comprehensive service tool capable of diagnosing, troubleshooting, and updating firmware remotely, reducing the dependency on service technicians and improving response time for customer issues.
Challenges and Solutions:
- Field Reliability Risks: Conducted an extensive DFMEA (Design Failure Mode and Effects Analysis) to ensure the service tool was fail-proof. Since the service tool was responsible for fixing malfunctioning chargers, it was critical that it never failed in the field.
- Seamless Integration: Ensured the service tool was fully compatible with SparkCharge’s existing V2 product line and adaptable to the upcoming V3 design for long-term sustainability.
- Remote Communication & Troubleshooting: Built a robust system that allowed real-time communication with deployed chargers, enabling remote diagnosis and over-the-air firmware updates.
Impact and Results:
- Improved Customer Retention: Enabled remote issue resolution, reducing downtime and increasing customer trust, leading to an 80% improvement in customer retention.
- Accelerated Project Timelines: Reduced the need for in-person troubleshooting, speeding up service and repair cycles by 30%.
- Cost Savings & Future Design Influence: Minimized service costs by reducing technician dispatches and influenced V3 product line design by incorporating enhanced serviceability features.
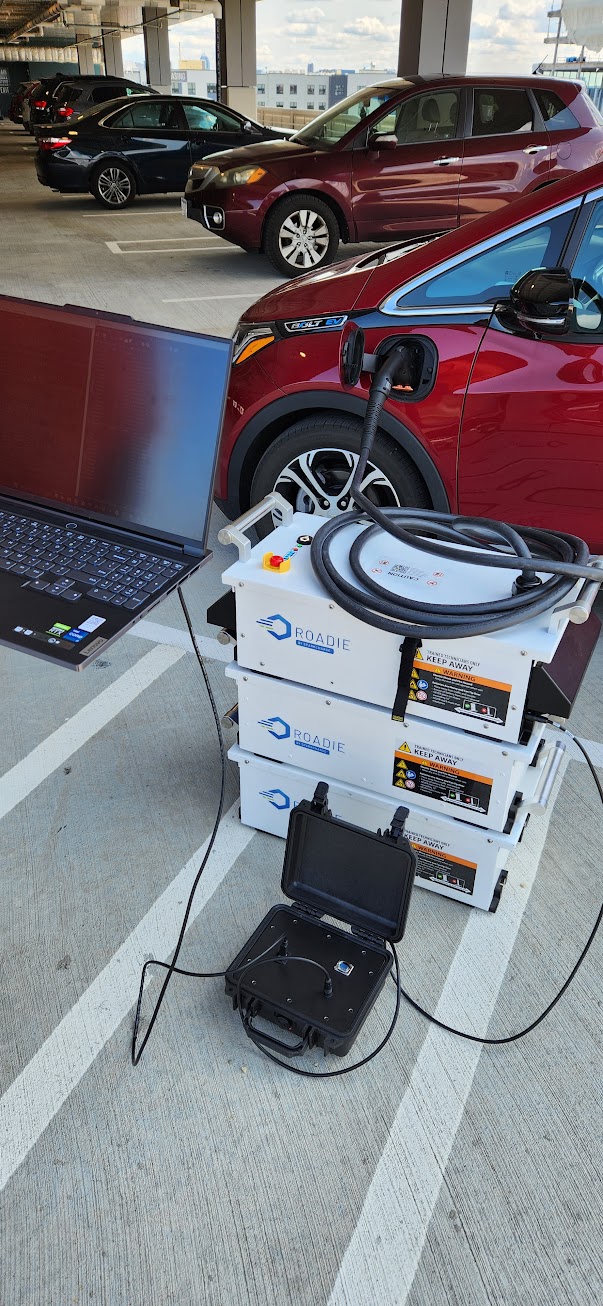
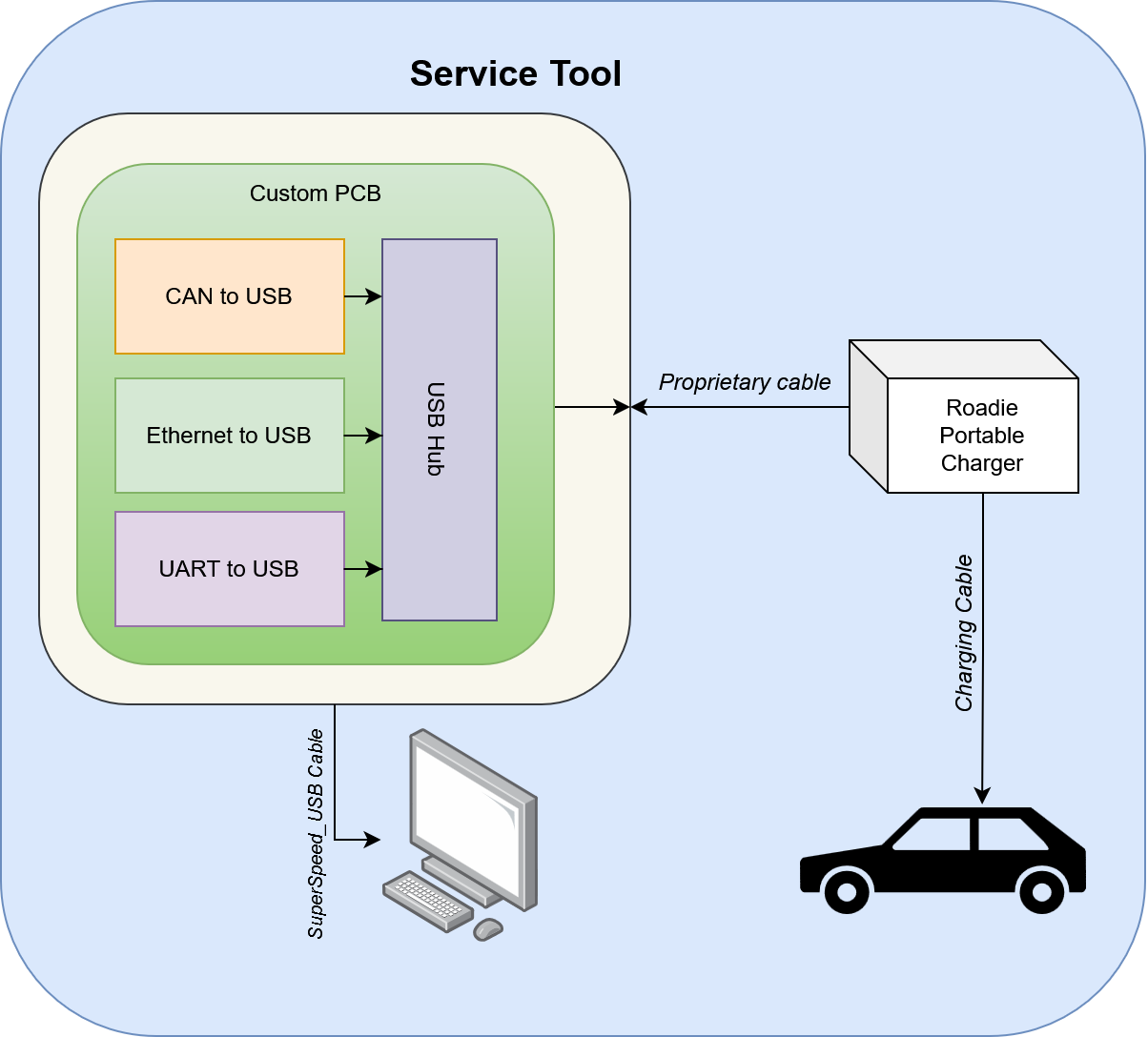